Hurricane Sandy picked up fish out of the Long Island Sound and dumped them into a pool on the Larchmont Yacht Club property. The storm of Oct. 29, 2012 also dropped pieces of trees and whole flaps of sod into the pool.
The most damage the club got was near a long outdoor banquet area, where large planks of wood were snapped and pointing skyward, according to Sean Murphy, vice president and operations director at Murphy Brothers Contracting Inc.
“It looked like someone took that and unzipped it,” he said. To repair the banquet area and adjacent building, the entire structure would need to be reworked and propped up temporarily to access underneath for flagstone and masonry work. “If we had a sky hook that would have been the best thing, but unfortunately that equipment doesn”™t exist,” he said.
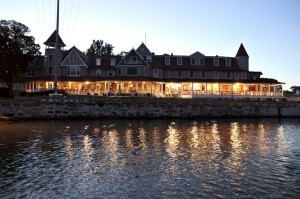
Murphy Brothers estimates 70 percent of its business is residential with 30 percent light commercial, mostly clubs like Larchmont. The targeted completion date for the work was the beginning of the 2013 outdoor season, April 14, an unmovable deadline in Murphy”™s view. “With clubs, you have to open on the day,” he said. “You can”™t tell 4,000 members, ”˜We need another week, you can”™t come here Memorial Day.”™”
Murphy Brothers did the repairs, met deadline and stayed on budget despite the intricacies of working at a century-old club with ancient wiring and piping and whose members respect the historical character of the structures.
The company knows Larchmont Yacht well, having done several renovations over the years to structures such as the club”™s Junior Jay building, bathhouses, and cabanas and suites. Each project is a bit of an adventure for the contractors as they bring renovations up to building code.
During some recent work, Murphy Brothers opened up a panel and found “knob and tube” construction, an early and often dangerous system for electrical wiring where single wires ran and were twisted around copper arms.
“We had never seen knob and tube before,” Murphy said. “We were ”˜shocked”™ to see them.” Unforeseen conditions in a historical structure could increase costs by as much as 5 to 10 percent, he noted. In older buildings, built when codes and regulation were not as stringent, there are often patchwork fixes or a hodgepodge of systems developed out of necessity over the life of a structure. Modernizing a structure while maintaining its classical feel is a challenge itself.
Perhaps the most challenging of the company”™s work at the yacht club was its latest, the $1.5 million job to open the veranda called the Quarterdeck. The club was founded in 1880, with the outdoor banquet area the Pandemonium added in 1902 and the Quarterdeck built in the early 1900s. The deck had been enclosed with siding and single-pane windows in a 1950s renovation to make it available for year-round use.
The company had to dismantle the entire Quarterdeck and rock-chip against the 1880s building abutting it, thereby expanding the basement beneath for an updated kitchen. Workers then rebuilt the entire porch on the same footprint, adding new mechanicals, spray-foam insulation and new mahogany floors and ceilings.
While working below the old Quarterdeck, workers found silverware that must have fallen through the cracks decades ago, according to Vincent Hackett, Murphy”™s senior project manager. “The Quarterdeck was so old, it was being held up by tree trunks,” he said.
Hackett said the group had the unique opportunity to make the structure “more traditional” by removing aspects of the renovation and having characteristics of the structure be consistent. For example, while temporarily removing support beams, Hackett decided it was best not to alter the structure drastically or even refinish or repaint. “I said we could clean these up but I don”™t think we should,” he said.
Capping off the new Quarterdeck are 180 feet of glass NanaWall doors, allowing for the space to transform from an enclosed area to an open veranda within an hour. The company also did a gut renovation to two adjacent club rooms and two kitchens.
The kitchen piece involved orchestra-like conducting by Hackett and the Murphy Brothers. The first kitchen to be renovated was on a floor above the other, which needed to remain operational even as pipes and wiring for the first kitchen had to be run through the lower structure. Hackett addressed this by working most with subcontractors when the kitchen was closed on Mondays and Tuesdays.
“We”™d come in there after the kitchen closed on Sunday and work for two days,” he said. As many as 30 or 40 people might be working on the kitchen at a given time including the chef whose input was as important as anyone involved.
Next on the agenda for Larchmont Yacht will be a Murphy Brothers-led construction-renovation of the tennis complex, complete with pro shop and bathrooms. And as far as future storms, the 11-acre property is more shored up for coastal flooding in extreme weather, a reality of work in the Sound Shore neighborhoods of Westchester.
Work on Larchmont Yacht”™s banquet hall left it better suited to withstand heavy-footed dancing. It used to be that when members and guests danced, the entire structure shook, sending ripples through beverages left on tables. Now, those beverages are ripple-free and in no risk of tipping over, Hackett said.
“The joke is they will save a lot of money on wine,” he said.