China manufactures 70 percent of the world”™s toys, according to IBIS World Market Research. A casual search of toys on the shelves of U.S. retail stores will find most of the items were made on the far side of the Pacific.
But at a recent trade association event for the toy industry, Fairfield County toy maker Jim Barber was surprised at the level of interest that several Chinese attendees showed for the items created by Luke”™s Toy Factory, the company he co-founded in Danbury. “It turns out these were the high-end Chinese, what we would call the 1 percent,” said Barber. “That”™s still a lot of people. They”™re the well-to-do of the Chinese people, where there is a cachet of having an American toy.”
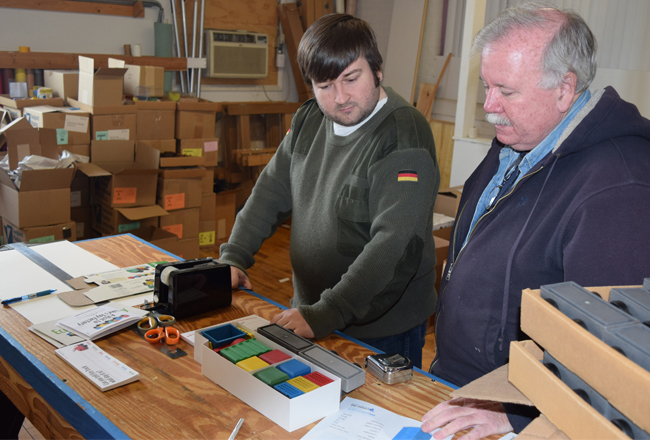
While Barber appreciated the positive attention from the Chinese, he was neither willing nor able to make an effort to penetrate China”™s toy market. “For us to ship to China, we can only be tested by a Chinese company, not an American company, and I have to pay for Chinese inspectors to fly from China over here to inspect the toys, which would be about $20,000,” he said. “And there is no guarantee that they will approve it, nor are there guidelines as to what they are looking for.”
If those Chinese toy inspectors made the trip to Danbury, they might be surprised to see Luke”™s Toy Factory headquarters at 128 E. Liberty St. Rather than a massive Chinese-style manufacturing plant, the company occupies a 1,500-square-foot walk-up loft in the rear of an industrial complex beside the Metro-North Railroad tracks.
“This used to be my commercial photography studio,” said Barber, who incorporated the toy company in 2012 with his son Luke and another father-son pair, Mitch and Evan Achiron. A White Plains resident, Mitch Achiron is a graphic artist and advertising design professional who continues to run Mitch Achiron Creative, the agency he founded in 1990. His son Evan is a marketing and communications professional.
Barber traced the company”™s founding to the 2007 recall by a suburban Chicago toy maker, RC2 Corp., of 1.5 million Thomas the Tank Engine Toys after their Chinese manufacturer was found to have used lead paint on them. Lead if eaten has long been known to cause neurological disorders in children that affect learning and behavior.
“I felt kind of betrayed by the toy companies,” Barber said. He began speaking with people in the industry and decided to go into the business. Startup funding for the venture came from a Kickstarter campaign that raised $15,000.
Five years after its launch, the four partners still comprise the company”™s total workforce. The Achirons are based offsite, with Mitch handling graphic designs and the company website and Evan in charge of public relations and social media marketing. Jim Barber manages daily business operations and Luke creates the toy designs and assembles each item by hand.
The company”™s product line is aimed at preschoolers and consists of four toy trucks ”” a fire truck, dump truck, cargo truck and tipper truck ”” that retail for $19.95 each.
The parts for each truck are of a standardized size, enabling the toy bodies and cab from each vehicle to be swapped with others and still fit in place. The company stresses safety for children and eco-friendliness, so the vehicles are paint-free and made of a wood plastic composite that combines virgin polypropylene with sawdust culled from furniture factories.
“When you have a recycled plastic,” Barber explained, “it”™s already been subjected to heat at least twice: first when it is pelletized and created as a resin and second when it is used for whatever use. With this (recycled plastic) material, it already has two heat events that happened to it, so it is possible there are additives that the original manufacturer didn”™t know about. There is no way to control it and I don”™t know what”™s in it from batch to batch.”
Luke”™s Toy Factory had used recycled resin, but discontinued that material because the company”™s injection molding vendor, Vanguard Plastics in Southington, had to clean its molds every eight hours when using it as opposed to every four or five days. “That costs them a lot of time and money, which translates into costing us a lot of time and money, so we aren”™t able to use that,” said Barber.
The product line is mostly found in independently owned toy stores ”” The Toy Room in Bethel was the first to carry the line ”” and small gift stores where the item can receive hands-on testing by its target customers.
Luke”™s Toy Factory sold approximately 6,000 toy trucks in 2017, double its 2016 retail sales volume. However, said Barber, “A major part of our business is wholesale, so if you put something into the wholesale chain you can”™t actually say that it was sold. In the spring, we”™ll see what re-orders are.”
Looking ahead for the next 12 months, Luke Barber is experimenting with roughly 25 different designs for product-line expansion, including a tugboat, barge, train set and an excavator. “Sometimes I can develop overnight from concept to basic version,” he said. “Sometimes it can take me much, much longer.”
The toy design work has been his only full-time job since he graduated from Rutgers University in 2012 with a degree in criminal justice. “I graduated at the worst time to be a criminal justice major, during the budget crunch when most of the police departments I was interested in working for were not hiring, but also downsizing their existing staff,” Barber said. “I am happy with the toy works.”
Also in the works this year is the company”™s new partnership with a pair of wholesale businesses serving the educational market, School Specialty and Kaplan Early Learning Co. The company is combining its toy trucks into a single package along with flash cards for teachers to show students how to assemble the items.
“Children between 2 1/2 and 4 years old are just learning fine motor skills,” Jim Barber said. “They are learning how to make their hands do what their brain wants them to do, which is put the toy together. The educational market is such a perfect fit for us. There is nothing else like it.”