Few cameras in history have borne the must-perform pressure of Neil Armstrong”™s Hasselblad, the first camera on the moon.
That same pressure ”“ including the Gs of liftoff and the airless, irradiated hell of the lunar surface ”“ rested squarely on the camera”™s battery. If that battery failed there would be, in non-NASA parlance, some explaining to do. The battery was a VARTA. It worked perfectly.
The Apollo XI need for reliable batteries has skyrocketed since 1969; today, there are 10 billion battery-driven devices.
VARTA Microbattery Inc., which on June 10 opened its North- and South American headquarters in the International Corporate Center at 555 Theodore Fremd Ave. in Rye, remains tethered to Apollo-like results, powering items as small as hearing aids with pea-sized disks and as large as entire homes with rechargeable lithium packs.
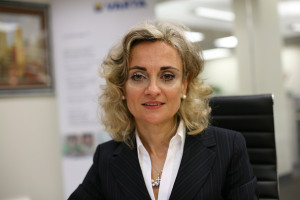
VARTA ”“ the name is a German acronym ”“ began in Germany 125 years ago providing basic alkaline batteries. The company today uses 13 different chemical reactions to store and deliver power, including batteries that produce a steady stream of pure hydrogen and others that can operate at low levels for long periods and provide spikes of intense power when needed.
According to Julia Palu, vice president for technical and marketing and also an MBA-holding electrical engineer, companies with a product idea approach VARTA about powering it. “The paradox,” she said, “is they want to devote less space to the power ”“ tuck it in as small a corner as possible ”“ while at the same time more power is needed.
“More energy density and more power, lasting longer in a smaller format, and now delivering high pulses of power, too ”“ how can we solve those challenges? The three things that come up most are: smaller, more powerful, longer lasting.”
VARTA”™s client list includes 13 car companies, 17 heavy equipment manufacturers, numerous medical device and security companies and even four large marine contractors. Its German-based corporate accountants cite annual sales of 400 million euros, or about $530 million. On June 12, the company expected to roll out its nickel-based rechargeable bicycle battery for the burgeoning “pedelec” market of battery-assisted bicycles.
The move to 6,250 square feet of office space in Rye follows three developments: American incorporation 40 years ago in Ohio, a 15-years-shuttered manufacturing plant in Elmsford and a smaller office in White Plains.
Today, manufacturing is done in China and Indonesia and the bulk of the engineering takes place in Ellwangen, Germany, where 150 scientists and engineers work for VARTA GmbH, the parent company, with 2,000 employees in total. The VARTA Microbattery division has been owned by Swiss-based Montana Tech Cos. AG since 2007, but remains linked to the VARTA parent company in name and staffing.
The new office adds a single sales position in the cross-county move, upping permanent staff ”“ dedicated to sales, engineering, project management, logistics and accounting ”“ to 20. William Flanagan is president and CEO of Varta Microbattery Inc. Palu has worked 20 years for the company.
Companies such as Hewlett-Packard look to VARTA to deliver products that embrace three quantifiable metrics, according to Palu: performance, safety and cost.
“We take the burden of power and solve it for them,” Palu said. “This enables them to bring to market high-performance and safe products.”
And, by all means, bring it on: “We are experts in designing systems that operate under extremely harsh conditions.”
Microbatteries now drive medical devices, security scanners, industrial machinery and the 10 billion electronic devices that H-P estimates now populate the world.
Hewlett-Packard teams with VARTA for the same reason as do Volkswagen, Caterpillar and dozens of other multinationals. “We work with H-P to enable them to reach their goals, providing them with the best devices so they can safely connect to the next 10 billion devices ”“ it”™s happening fast,” Palu said. “In a mission like medical field devices, where safety and performance are paramount, our reputation is built on quality on a consistent basis. These things cannot fail while performing their duties.”
If they cannot fail, neither can they in the modern world pollute. VARTA today makes all of its cells without mercury, the long-serving toxic workhorse of batteries.
VARTA batteries must function in explosive environments, in watery environments, even in the “cold soak” of outer space.
Palu said large computer servers provide a VARTA market and an example of specific needs. “The servers function at 45 to 50 degrees centigrade,” she said. “Lithium-ion batteries cannot charge above 45 degrees centigrade and cannot discharge above 65 degrees. Our nickel-based batteries can charge to 70 degrees centigrade and discharge up to 85 degrees (185 degrees Fahrenheit). Servers are an extremely tough environment for batteries and the system must operate for a minimum of three years without interruption, backing up data. Reliability is a huge factor.”
Some batteries will be sealed into their units with task-specific gaskets ”“ gasket work is contracted out ”“ and must recharge themselves even while discharging.
VARTA power sources run the gamut from its Power One hearing aid microbatteries ”“ the most popular in the world, according to Palu ”“ to solar energy caches that can outlast the darkness. In Europe the company is already engaged in a program envisioning large storage units for basements hooked only to solar cells on rooftops. “A perfect energy loop,” Palu said.
One VARTA battery, the H2 cell, manufactures tiny clouds of pure hydrogen to propel liquids and granular compounds. “Even scents,” Palu said.
And the future looks ”¦ powered. “H-P believes the next 10-billion devices are right around the corner,” Palu said.
You could be wearing some of those devices. VARTA through November joins Swiss-based ST Microelectronics and Dallas-based Texas Instruments for the “Wearable Technologies Innovation World Cup,” in which contestants vie in six categories, including sports and health care, to wire and power clothing.
The effects were developed by Dr Kapil Sugand, who works at St George’s Hospital and Imperial College London, and Dr Pedro Campos from St George’s Hospital.
The animations are not true holograms, but are rather based on an illusion called Pepper’s Ghost which uses glass or foil combined with special lighting techniques to make objects appear in mid-air.
They said they wanted to make it easier for students to absorb the large amount of detail necessary to pass their exams. Medical students can attend up to nine hours of lectures per day and typically study for six years in order to qualify.
“Research in educational sciences has shown the attention span of the average student is 20 to 30 minutes, but standard lectures are at least an hour,” Dr Sugand told the BBC.
You can read more at:
http://www.sesjalinuksowa.pl
http://www.effectivedevelopment.pl
http://www.projekty–domow.pl
An animation was used in the test lecture to illustrate how fluid passes through a kidney
“The human body is a very complex machine. It’s very difficult to comprehend and appreciate how a kidney or liver functions, for example, from Powerpoint slides.”
The images are all animated and can be controlled by the lecturer.
Three projectors are used to generate the full colour images on stage and they are designed to be used in a large auditorium.
The pair have spent L10,000 building up a small library of 3D animation lecture aids – including a sequence which outlines the various effects of malaria on different parts of the human body.
http://www.ofertbank.pl
http://www.xpress.org.pl