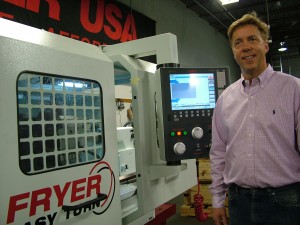
Larry and Elizabeth Fryer had no backyard garage in which to tinker in 1982 ”“ Scarsdale”™s Garth Road where they lived was (and remains) cheek-by-jowl with apartments. So they put a second, unused bedroom to use to begin Fryer Machine Systems Inc.
Today, the Putnam County company is at the forefront of what its owner calls “a resurgence in the manufacturing economy that presents us with a real opportunity to step up.”
Originally, the Fryers distributed machines. They shifted to manufacturing ”“ believing they could build a better machine, as Larry put it ”“ and now their company manufactures a dozen different series of spinning lathes and cutting mills that make parts for other machines.
A recent Fryer sale to Boeing answered the aircraft manufacturer”™s need to custom make air-conditioning conduits for its jets. Fryer”™s machine categories include vertical and horizontal production machines, turning production machines, five-axis machines and tool room machines for either turning or milling.
Larry Fryer demonstrated a five-axis machine with his telephone, showing how it could work on multiple faces of the phone at once. “Most machines work on a single axis, so you have to pull out the piece and turn it and start the machine and do it again and again,” he said. “This is a real time-saver. It reduces labor and allows a company to compete with low-wage-labor countries.”
Customers include Ball Chain Manufacturing and Crown Die Casting, both in Mount Vernon; Farrand Controls in Valhalla; Kimber Manufacturing in Yonkers; Goodrich Corp. and New Machine Company, both in Danbury, Conn.
“The secret to our success is continuously investing in more technology,” Fryer said.
Saving time saves money and Fryer said the U.S. manufacturing base is looking like “a bargain” regarding manufacturing costs when compared with Europe, which has higher per-worker costs. “Foreign nationals are now coming to us to manufacture in the U.S. because of a skilled workforce and relatively low wages. Believe it or not, we”™re a bargain compared with Europe.”
Fryer sells 300 to 400 units per year globally, Fryer said while leading a tour of his Jon Barrett Road facility in Patterson.
If you ever spun the leg of a stool on a woodshop lathe or filed a machine part to fit, this is an entirely different world of machinery. For starters, Fryer machinery more closely resemble giant medical equipment than tools associated with making things. The kitchen-clean manufacturing floor contains a part-making shop, a fully sealed paint room, a parts department, an electronic assembly area and a separate sign shop. The sign shop reflects the fact Fryer builds so many custom machines; the Indian textile manufacturer and The Boeing Co. do not require the same technical readouts, but each must know where the emergency shut off is located.
Fryer uses 35,000 square feet at its headquarters and rents another 13,000 square feet to two unrelated companies. When the economy tanked after the Sept. 11 terrorist attacks, Fryer contracted to several inner offices, a point at which Fryer said he discovered the economic value of being a landlord.
But business has picked up again to the degree Fryer said recently, “I don”™t think we”™ve ever been this busy.”
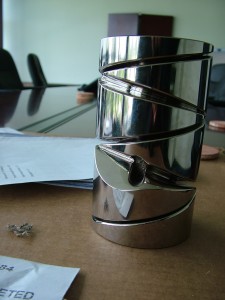
“We can”™t build them fast enough,” Sue Ostrander, the company”™s marketing director, agreed. The pair was seated at the company”™s conference table, which was doubling to hold piston-like machine bobbins ”“ for a proposal to have Fryer build a machine that could in turn build the shiny pistons on display. And, a point stressed by both Ostrander and Fryer, the company by design uses as many local materials and vendors as possible. “We contract out to a lot of small machine shops for parts,” she said.
The headquarters”™ polished-stone floor and thermal windows are local, too, and the building taps free underground heat via a geothermal design, all via Pound Ridge architect Lucio DiLeo.
Ostrander said Fryer”™s mission and its success come down to three critical points:
”¢ Fryer is one of just a few American manufacturers who hand-make machines rather than serving as mere distributors. “It”™s very rare to find hand builders of machines and the result is our machines are much more tested than machines that are mass produced,” she said. The company does, however, employ some 30 North American distributors and international distributors in Russia, Poland, New Zealand, Australia and Costa Rica;
Ӣ Fryer has partnered with German manufacturing and engineering giant Siemens AG on its Touch 2100 touch-screen that customizes digital control screens; and,
Ӣ Fryer custom makes machines, as for the Indian textile concern that demands its oversized bobbins be microscopically smooth to prevent burrs from snagging yarn.
Fryer said, “The customer who currently uses three machines for a process can now use one.” This was the case with Boeing, which after consulting with Fryer engineers, bought a single machine that replaced a trio of lesser machines.
Fryer teaches about its machines in a classroom setting and offers a full-scale service department headed by Rich Cicero. “Vital” was Fryer”™s word describing Cicero”™s function. The company employs 35.
The website is fryermachine.com.