Commerce Packaging Corp. recently shipped a 5,000-pound electronics package to Dubai.
The Dubai-bound crate was still open while principals Mickey Alexander, father, and Jeff Alexander, son, pointed to details of the craft of custom shipping, which factors carpentry, physics, engineering and materials science with carved-in-stone delivery dates. When 10 tons or a few critical ounces absolutely, positively has to get there ”” perhaps in packaging certifiably free of microbes ”” Commerce Packaging offers a shipping solution.
“The only thing fixed is the delivery date,” Mickey Alexander, 71 and a Michigan State-educated engineer, said of Commerce”™s deadline-driven business. “There can be problems with manufacturing, with testing, delays along the supply chain, but the delivery date is the delivery date. It does not change.”
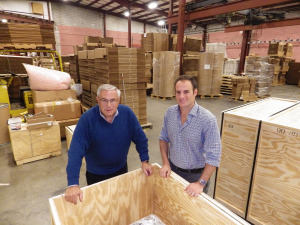
Jeff Alexander, 40, with an MBA from New York University, said that, as such, the company stocks the required materials for unusual jobs and is ready to pack and ship when the client calls. “We just did a Sunday job like that,” he said.
In 2000, Commerce Packaging consolidated its four offices, including a Stamford presence dating to 1954, at 305 Wilson Ave. in Norwalk, across from the SoNo Ice House skating facility. The 70,000-square-foot site hosts Commerce”™s manufacturing and warehouse space and administrative offices, plus active loading docks for six to 10 company vehicles, including an 18-wheeler.
“This shipment has to handle a lot of different environments,” Mickey Alexander said of the Dubai crate. “Not just the air environment ”” it”™s protected from that, of course. Then there is motion on highways, motion on rolling seas and forklift handling. These can be critical and expensive parts. They can be integral
components to larger systems, like power plants and U.S. Navy vessels.”
About 35 percent of the company”™s business is nonlethal military in nature ””mechanical generator sets and mechanized vehicles typically ”” down substantially from when the company employed 220 during the Vietnam War. The lesser uptick in military shipping from the Persian Gulf conflicts ended two years ago, Mickey said. Commerce Packaging employs 30 today.
Getting the product from the manufacturer to the manufacturer”™s client on time and unbroken presents limitless variables. A 2-foot-tall aerosol can-manufacturing unit was ready for shipment recently, for example. It was a teched-out knot of tubes and valves crossed with a drill press, and its customized shipping box was being built. Mickey Alexander called it “a pretty typical delivery.”
The shop uses wood of different species, foam of different densities and “corrugated” ”” commonly called corrugated cardboard ”” of different strengths.
Fans of Tom Wolfe”™s “Bonfire of the Vanities” would note the industrial bags of foam peanuts in the facility. Both father and son affirm the company effort to use natural products, but the peanuts continue to be popular for usefulness and cost. Other foams are selected for specific densities for specific jobs and are cut on a specially bladed band saw that could cut a small car in half.
“Peanuts, staples, glue,” Mickey said. “We can do 10 by 10 by 10, inches or feet.” A crate-in-the-making could have held Paul Bunyan”™s ax: 2 feet wide and 23 feet long.
“Optionality” was the word Jeff used to describe Commerce”™s ship-anything ethos.
The company even handles individual customers. “I call it wholesale to the public,” Mickey said. “If someone comes in, they get treated like a customer.”
“My grandfather said, ”˜We sell service,”™” Jeff said. “Our two-by-fours come from the same trees as our competitors”™. The same foams are available. The only thing we can do is provide better service. It really comes down the service.”
In the case of 5,000 pounds of electronics heading to Dubai, that meant gasketing, sealing and evacuating the air and then crating the goods in heat-treated plywood and spruce.
“Our forte is that we can integrate the three different materials ”” wood, corrugated and foam ”“ from this one source,” Jeff said. “We have optionalities of size and quantity.”
The company this year celebrates 60 years since Stanley Alexander, who died in 1997, founded it. A tour of the company”™s 14-year-old Norwalk facility revealed packaging varied in size for products, from individual nuts and bolts to containers for brass mixing vats measuring  up to 15 feet. A set of hardwood skids was just built to accommodate an 18,000-pound load. Commerce notably packed and shipped parts for the Hubble Space Telescope.
To ship as broadly as it does, the company endures monthly anti-pathogen government inspections. The official “HT” stamps on its wood mean “heat treated.”
Neither father nor son went directly from college to the business. Mickey worked for a packaging and tin-can concern in New York before coming to work for Stanley Alexander. Jeff, who said he always knew he would return to the family business where he had worked as a youth, left Wall Street for Commerce in 2011.
The company maintains a sales force of four. Jeff said Commerce is countering business downticks by aggressively marketing itself in an expanded footprint: Connecticut to the Massachusetts border and into Massachusetts, Westchester County and Long Island in New York, plus northern New Jersey. About 75 percent of company”™s contracts are in-state, with Westchester County its next-biggest market.