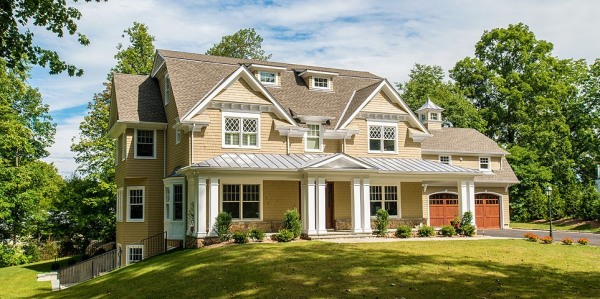
After he had offered comments for a story on a very different way to heat and cool homes, Salvatore Zarrella, principal of Construction Management Group LLC in New Canaan, offered a testimonial that buttressed his enthusiasm for the concept. “We were just informed yesterday that Construction Management Group received the Home Builders and Remodelers Association of Connecticut Inc.”™s HOBI Award for 2014 in the categories Best Build In Town Custom Home and for Best New Construction Technology,” he said.
“It”™s a very good construction story,” Zarrella said of his embrace of ceiling-based temperature controls in a home. “There isn”™t anything out there like it.” Zarrella has completed work on a radiant-panel home on Orchard Lane in New Canaan, the first such heating job east of California, where three such homes have been built, he said.
Radiant heat is not new, typically rising from the floor via a latticework of hot-water tubing beneath the flooring. The twist in Zarrella”™s equation places the panels in the ceiling.
“It is absolutely the wave of the future,” Zarrella said. “Radiant heating in floors has dominated the radiant heating industry for a very long time and has been very effective at distributing heat. However, it has some very specific drawbacks compared to this approach.
“All the panels are in the ceiling,” he said of the new design. “We did extensive research before endorsing and recommending the system to my client at 25 Orchard Lane, which recently finished construction, a new in-town home here in New Canaan.”
Andrew Nuzzi Architects LLC in Stamford was the Orchard Lane architect. An architect, a high-end location, a technology untested outside California ”¦ how is it going?
“I was a little nervous but it is more successful than we could have imagined and has been through both heating and cooling season and passed with flying colors,” Zarrella said. “It has proven to be far superior to any system I have ever installed in our new home construction projects.”
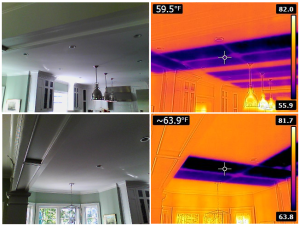
How does typical radiant heat work?
“Typical radiant heating has been just that, just heating; it requires a separate system for cooling altogether. This means extensive ductwork in addition to all the work that just went into the radiant floor. If you want multiple zones, typically that means separate air handlers and separate equipment. This also typically means you need multiple compressors outside (the outdoor units are referred to as the condensers). The average 5,000-square-foot home sometimes has two to four units outside to accommodate different zones in the house. This is unsightly and takes up lots of space outdoors, eating up the yard and the local zoning tolerances. Typically, the average house has a master bedroom zone and main bedroom zone on one air handler (with a zone damper). The main floor is typically one zone and one zone for the basement. Control is limited to the number of air handlers and is often problematic. You can have large temperature swings from one room to the other with little control.”
Zarrella cited other drawbacks to conventional radiant heat that included furniture and carpets as heat-blocking insulators, restrictive flooring choices and the common problem of repair jobs that puncture the water tubes in the floor. “The risk of puncture is significantly minimized,” he said of the ceiling units. “And if they somehow do get punctured, the repair is very easy to make as it just requires a few simple fittings and patching drywall. Repairs are inexpensive.”
What is your experience with the new system?
“The home at 25 Orchard Lane has one outdoor unit that handles both heating and cooling,” he said. “Most 5,000-plus-square-feet houses need more than that, sometimes three or four units. There are no air handlers in the house except for the fresh air system providing fresh air to the house with minimal duct work.
“It”™s simple: In the winter time we push warm water through the radiant panels and in the summer time, through those same tubes, we push chilled water. Furthermore, additional equipment is not necessary; the mechanical equipment used for the cooling source is the same as the heating source.
“The Orchard Lane home has one thermostat/sensor for every room ”“ 21 total. That mean 21 individual rooms controlled independently creating total control ”“ unheard of conventionally. As a standard feature, all these rooms can be controlled remotely outside the home through the internet.”
Zarrella said the panel system is 20 percent to 40 percent cheaper to run than conventional forced air systems and gets “much more” thermal output than typical radiant floors. “For even greater efficiency, solar hot water collectors can easily be introduced to make it super efficient,” he said. “Then there are tax benefits.”
Zarrella also cited health benefits, calling the system “healthier and more comfortable than any other system available by far.”
He said the cost of installation is comparable to that of a radiant floor system, but its ease of use ”“ less ducting ”“ reduced the construction time on Orchard Lane by a month.
CMG also received the 2013 Home Building Industry Award for Best Custom Home (5,000 square feet to 6,000 square feet), and is presently conducting all renovation and restoration work at United Methodist Church in New Canaan.