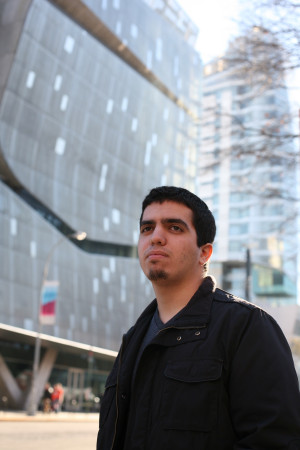
With Purchase College on winter break, student and startup entrepreneur Shai Schechter was back home on Staten Island when the Business Journal called. He agreed to meet us in the East Village across from Cooper Union, where three of his business partners study engineering.
We were about a block away from a partner”™s apartment where their company”™s product prototype was stored. We wouldn”™t be able to see it, though, since the tenant and keeper of the prototype was traveling in Israel during Cooper Union”™s winter break.
Their product is Deltaprintr, a mechanically and structurally minimalist, high-resolution desktop 3-D printer whose youthful developers are marketing at student-friendly, school-budget-accommodating price points. It”™s an educational tool, Schechter said, and the startup already has had interest from some high schools and middle schools in the company”™s initial target market.
Over their summer break, the partners will assemble and ship an initial production run, including at least 100 do-it-yourself kits priced at $499. An assembled printer is priced at $685 or $705, depending on size. By comparison, most commercially sold printers cost $2,000 or more.
To cover startup production costs for 200 printers, Schechter and his partners in early December set out to raise $195,000 from backers on Kickstarter. With four days left in their online campaign, they had long passed their goal, having raised $224,000 from 633 backers.
With 100 of their build-it-yourself printers offered to Kickstarter pledge-makers, “The kits sold out in two to three days,” Schechter said at a table in Ray”™s Pizza Bagel Café on St. Mark”™s Place. The assembled printer was slower to sell until the partners added a taller model that allows for larger objects to be printed. “Those were sold out in a week or so,” he said.
Deltaprintr”™s founding brain trust was careful to limit the number of pledges accepted at various dollar levels in order to limit its initial production volume and be able to meet demand. Venturing onto Kickstarter, “You don”™t know what”™s going to happen,” Schechter said. “You hope for the best, but not too much the best.”
These students have received plenty of publicity on tech blogs and websites like Engadget and Mashable since the Kickstarter launch. Even before the launch, they had already drawn about 2,000 subscribers to their Deltaprintr website. “There”™s a whole open source community behind these hobbyist printers,” Schechter said. The Deltaprintr entrepreneurs are part of that, using open source software and firmware for their product.
Their Kickstarter business story has been picked up too by the international mainstream press, reaching potential customers in distant places through the Sydney Herald in Australia and the Press Trust of India.
They”™ve said no to some requests for network television interviews in New York. “We don”™t want to overreach ourselves,” Schechter told me, and end up unable to fill the many orders that more publicity might beget, “so that”™s why we turned down their offers.”
A native of Israel who immigrated with his family to New York about 13 years ago, Schechter is a 21-year-old junior on the SUNY campus in Purchase pursuing a major in graphic design and a minor in arts management. He also happens to be a compulsive tinkerer, one of those kids who borrowed his dad”™s tools to take apart household gadgets and appliances ”“ and sometimes even put them back together again.
“I”™ve been into 3-D printing for a while,” he said. “Anything with new technology, I”™m really on top of it.”
Additive manufacturing, as 3-D printing also is called, makes three-dimensional objects from digital models. As Schechter himself described it in a press release from his college, it “brings the manufacturing back home. You buy the material in a spool, as a continuous string of plastic. The hot-end is like a hot glue gun that moves very precisely, printing out the object layer by layer according to the program that is input. It can be used to print out a whole range of objects, from simple household items, to sculptures, to prosthetic hands specified to someone”™s dimensions.”
“This whole thing started with my school and realizing they can”™t afford a 3-D printer,” Schechter told us.
In his sculpture class at Purchase, students operated a printer that Schechter said was “not good” for educational uses. “It”™s really expensive to use,” he said. “It costs about $500 for a bucket of powder,” the material used to build objects in some 3-D printers. “Those buckets only last for about two prints or so.”
Schechter told his sculpture professor, Eric Wildrick, that he could build a more effective and simpler plastic printer for classes. Wildrick asked him to write a project proposal to submit to Ravi Rajan, dean of the college”™s School of Arts. Schechter did so, and the college awarded him a $1,000 grant to build his printer in an independent study project overseen by his professor.
“There”™s definitely demand for it at educational institutions,” Schechter said. The do-it-yourself kit and Deltaprintr assembly manual make a student”™s encounter with 3-D printing even more educational. Building your own, “It”™s a lot easier to understand how it works that way.”
His college project was only a primitive version of the 3-D printer that Schechter later developed with friends who he”™s known for a decade from summers spent at a family resort community in the Poconos. The team includes Cooper Union students majoring in civil, mechanical and electrical engineering, and a math and finance whiz attending Williams College.
“When you start a business, you recruit people who are smarter than you at something,” Schechter said. “That”™s how you grow a business. That”™s how we”™ve been growing over time, slowly but surely.”
Departing from the box design of most commercial printers, the Deltaprintr is a simple open construction supported by three aluminum poles. Schechter and his team of tinkerers replaced belts with high-strength fishing line to move the print head, which allows for larger prints and easier replacement.
The partners last summer began researching and lining up price quotes from manufacturers and supply sources in China and the U.S. In May, they expect to begin test production.
“We”™re going to assemble them ourselves,” said Schechter, who is looking to lease 500 to 1,000 square feet of commercial space in Staten Island or Brooklyn. “It will be a labor-intensive summer.”
“Hopefully people put in the time and dedication to assembling them. That”™s what we”™re looking to offer. Our main goal is to keep them affordable for students like ourselves.”
Like building a 3-D printer, starting one”™s own business is a learning experience that Schechter highly recommends. “You learn so much more when you start your own business than you do in school,” he said. “If you”™re really passionate about learning something, you can just go and do it on your own.”
Yet this budding entrepreneur is not quite ready to follow in the footsteps of such notable college dropouts as billionaires Bill Gates and Mark Zuckerberg. He”™ll return to Purchase later this month for the start of the spring semester.
“There”™s a certain limit to how much you can learn on your own,” he said. “You still need the real-world experience that professors have.”
Come September? His senior year at Purchase College might have to wait.
“We”™re going to see where this goes,” he said.
This guy […] never built anything he used the 1000 dollars to buy a 3d printer kit and assembly it to be used with lot’s of glitches in each use, not able to asses what do to fix printing problems like supports, and stuck to the bottom of the printer. he rarely printed things and never 3d modeled things only printing things from thingiverse ugh no