Terex revving up new diesel engines
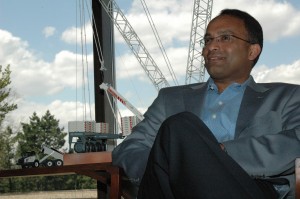
Even as fuel prices dramatically escalate this spring, Terex Corp. and other companies are finalizing plans for new engines that promise an even more dramatic cut in harmful diesel exhaust.
The Westport-based company makes a range of heavy construction vehicles and equipment. In a transaction potentially worth $1.3 billion announced in late April, Terex launched a public tender offer to acquire Demag Cranes AG of Dusseldorf, Germany. In 2002, Terex acquired Demag”™s mobile crane division.
Both the U.S. Environmental Protection Agency and European regulators are requiring diesel engine makers to scrub out nitrogen oxides and particulate matter from emissions. The EPA says the measures will reduce harmful diesel emissions by 90 percent; the Connecticut Fund for the Environment cites statistics suggesting that diesel fumes contribute to 4,000 asthma attacks in Connecticut each year ”“ and 200 deaths on average annually from heart attacks or other causes.
First proposed in 2004, the EPA has given the industry a decade to make the conversion in multiple phases, with the current Tier-4 implementation date looming for 2014, a deadline Terex indicated it will meet.
The change comes even as fleet operators absorb big increases in the cost of diesel, which as of May 2 was $4.23 a gallon on average in New England, up more than a dollar from a year earlier according to data compiled by the U.S. Energy Information Administration.
Some companies like Greenwich-based United Rentals Inc. have been able to offset some of those costs with financial hedging instruments.
In a conference call with investment analysts to review Terex”™s first-quarter results ”“ the company earned its first profit in a year at $5 million as revenue rose 34 percent to $1.3 billion ”“ Terex CEO Ronald DeFeo said the company is applying tax credits to help cover at least some of the cost of converting its engines to be Tier-4 compliant.
“The bigger the equipment, the more we”™re into the Tier-4 interim products,” DeFeo said. “That would include product lines like materials processing (and) our articulated trucks, the bigger, rigid trucks that we sell ”¦ We expect the mid-sized products to go full bore into the Tier 4 in 2012. So it”™s a process that will go through our product line: 2011, biggest equipment; 2012, mid-sized equipment; and then we get through that by probably ”˜13 and ”˜14.”
The tiered process has helped conglomerates like Terex immensely, whose extensive product line has required significant reengineering ”“ possibly at the expense of some product development that might otherwise have occurred.
“They didn”™t want to make such a big quantum technology jump so that the technology cost and implementation would be so substantial,” said Jacob Thomas, senior vice president of product development and marketing for Terex. “This was very quickly my No. 1 priority when I joined (Terex) in 2007.”
Terex is now buying engines equipped with two differing diesel-reduction systems, depending on how the engine is used.
One system reduces nitrogen oxides by cooling exhaust and circulating it back through the engine during the combustion process. While this process increases the amount of particulate matter in the final exhaust gas, a filter is situated to trap those particles, with the filter of course requiring periodic replacement. One challenge ”“ such exhaust-gas recirculation systems require ultra-low sulfur fuel, which is not readily available in some countries.
That system also only works in engines that run continuously, such as trucks, as exhaust gases must be hot for the process to work. For engines that do not heat up ”“ for instance aerial lifts ”“ Terex is employing a second technology called selective catalytic reduction, in which higher fuel injection pressure helps reduce particulate matter, and nitrogen oxides are handled with the help of a separate additive called diesel exhaust fluid that requires its own tank. In the catalytic converter, the fluid ”“ which again is not yet distributed widely ”“ breaks down nitrogen oxides into harmless nitrogen and water vapor.
Until last year, Fairfield County was the home of Clean Diesel Technologies Inc., which is developing techniques to solve the both nitrogen oxides and particulate matter emissions. Following its merger with Catalytic Solutions, the company relocated its headquarters to California, which has been at the forefront of state efforts to regulate diesel emissions.
“The holy grail for the diesel manufacturers is not to have to use all these different technologies to solve these problems,” Thomas said. “Whether you take the filter or the exhaust, it is an event that happens after the fuel has been combusted. The ideal is that the exhaust that comes out of the fuel itself is clean.”